Implementing ISO 13485: A Step-by-Step Guide
- Home
- Blog
Categories
Latest Post
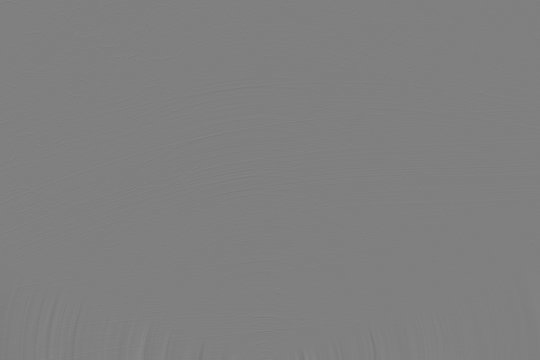
ISO 14001 Lead Auditor Course
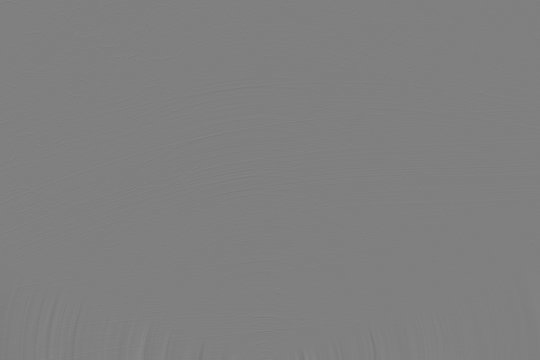
ISO 14001 Foundations Course
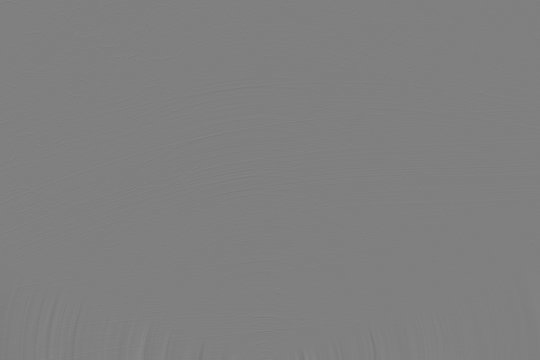
ISO 14001 Internal Auditor Course
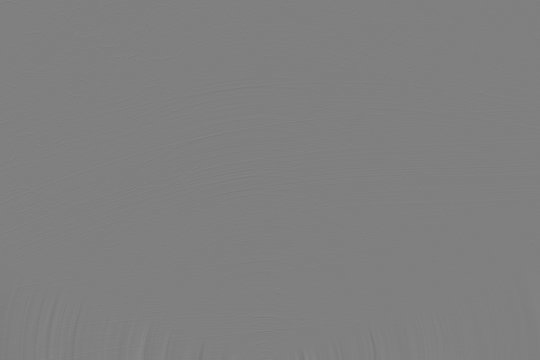
ISO 14001 Lead Implementer Course
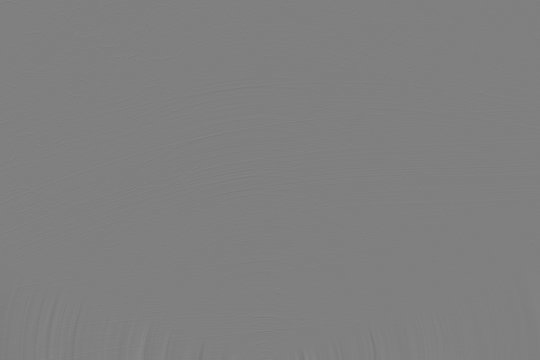
Thinking about implementing a Quality Management System (QMS) and getting certified against ISO 13485? This guide will help you understand the steps involved and common pitfalls to avoid.
Benefits of ISO 13485 Implementation
Meeting regulatory requirements and ensuring patient safety are critical for maintaining consistent medical device quality. Compliance with relevant standards guarantees an appropriate level of quality control. ISO 13485 is a well-established international standard for Quality Management Systems in the medical device industry. Achieving certification demonstrates adherence to best practices and regulatory requirements, leading to better control over processes, continual improvement, and a positive return on investment.
Why Implement ISO 13485?
Improve Company Credibility and Image: Certification demonstrates adherence to best practices.
Enhance Customer Satisfaction: Ensures products meet customer needs.
Improve Processes: Streamlines and optimizes operations.
Better Decision-Making: Based on reliable data and processes.
Foster a Culture of Continual Improvement: Encourages ongoing enhancements.
Engage Employees: Involves staff in quality initiatives.
Steps to Implement ISO 13485
1. Get Management Support Without management support, your ISO 13485 implementation project is likely to fail. Present the benefits clearly and get your management team on board from the start.
2. Identify Requirements Understand all the requirements your QMS needs to satisfy, including legal, regulatory, customer, and other requirements based on your company’s needs and culture.
3. Define the Scope of Your ISO 13485 Implementation Avoid applying the QMS to non-quality areas but ensure the scope is beneficial. Note that ISO 13485 is only applicable to the manufacturing of medical devices.
4. Define Processes and Procedures ISO 13485 defines mandatory procedures for your QMS. Determine additional processes and procedures necessary for consistent quality. Define all processes and see how they interact, as interactions often reveal problems.
5. Implement Processes and Procedures Document existing processes and procedures to ensure consistent quality. Not all processes need documentation, but critical ones do to guarantee consistency.
6. Deploy Training and Awareness Programs Ensure every employee understands the QMS and their role within it. Train all personnel on the basics of ISO 13485 and any process changes. Timely training is crucial for successful implementation.
7. Choose a Certification Body The right certification body will audit your QMS to determine conformity with ISO 13485 requirements and assess its effectiveness and continual improvement.
8. Operate the QMS / Measure the System Collect records required for audits to show compliance and effectiveness. This period usually lasts two to three months.
9. Conduct Internal Audits Perform internal audits of each process to identify and correct issues before the certification body conducts its audit.
10. Conduct Management Review Management must stay involved in the QMS’s ongoing maintenance. Review data from QMS activities to ensure processes have necessary resources and are improving.
11. Take Corrective Action Identify the root cause of problems discovered in audits and reviews, and take necessary action to correct them. This step is crucial for continual improvement.
12. Perform the Certification Audit Auditors from your chosen certification body will review your documentation to verify that all ISO 13485 requirements have been addressed in your QMS.
Common Pitfalls When Implementing ISO 13485
Inadequate Understanding of Requirements: This can lead to incomplete or incorrect implementation, resulting in certification delays or failure.
Assuming All Requirements Apply: Not all ISO 13485 requirements apply to every process. Exclude non-relevant clauses as necessary.
Inadequate Employee Training and Awareness: Ensure all employees understand the requirements and their roles within the QMS.